 |
Re-examining the Opportunities for Gigabit Ethernet in
PC-based Machine Vision Systems
|
|
With the release of the new UNO-3072LA Embedded Automation Computer with two Gigabit Ethernet ports and PCI interfaces, we re-examine the opportunities for such devices in Machine Automation. Industrial equipment suppliers and manufacturers are always looking to increase throughput while increasing product quality, ensuring that machine vision continues to play an important role in maximizing productivity, efficiency, and quality. With the help of Gigabit Ethernet, levels of performance and flexibility are being achieved that were not possible as recently as a few years ago.
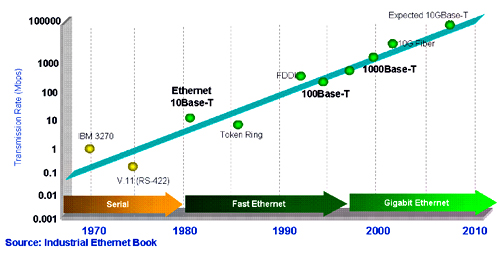
For those not familiar with the term Machine Vision, it is the application of computer image processing to industry and manufacturing. Overwhelmingly, it is the preferred means for visual inspections that require high-speed, high-magnification, repetitive operation, and repeatability of measurements.
Traditionally, these systems have been based on analog cameras or commercial technologies not well adapted to the needs of industrial systems. Such systems generally consist of an analog camera connected to a special PC-installed interface card (called a “frame grabber”) or a first generation digital camera connected via CameraLink™, USB or FireWire™ (IEEE 1394) interface. Often, special lighting is often required, which generally consists of a strobe light, triggered by an external photoelectric sensor.
While acceptable for office, laboratory, and light industrial environments, these technologies are not well suited for industrial applications. First and foremost, distance limitations of 5m to 10m for analog and first generation digital cameras limit the use of machine vision to small systems, or worse, they compromise the location of the PC, putting it in a location that may cause premature failure or that is difficult to service and maintain. Finally, the use of proprietary interfaces and the lack of standardization between component manufacturers make it difficult, if not impossible, to select best of breed components and successfully integrate them into vision systems.
These obstacles and the emergence of Gigabit Ethernet prompted a number of camera manufacturers to work with the Automated Imaging Association to develop the standard now known as Gig-E Vision. This new standard allows extremely fast image transfer, over relatively long distances, using low cost standardized cables. It also allows seamless operability between hardware and software from different manufactures, with a more flexible architecture, and the ability to scale with the technological advancement of Ethernet.
|
|
GigE |
1394b |
USB 2.0 |
Camera Link TM |
Type of Standard |
Commercial |
Consumer |
Consumer |
Commercial |
Connection Type |
Point-to-point or LAN - Link (RJ-45/Cat-5) |
Peer-to-Peer - Sharred bus (4/6 pin STP) |
Master-slave -Shared bus (4 pin STP) |
Point-to-point - Link (MDR 26 pin) |
Performance |
< 1000 Mb/s
Continuous Mode |
<800 Mb/S (but only 512 Mb/s for image data)
Continuous Mode |
< 12 Mb/s; USB1
< 480 Mb/s; USB2
Burst Mode |
< 2380 Mb/s; Base
< 4760 Mb/s; Med
< 7,140 Mb/s; Full
Continuous Mode |
Distance - max with switch - max with fiber |
< 100 m (no switch)
No limit
No limit
|
< 4.5 m
72 m
200 m |
< 5 m
30 m
|
<10 m |
Scalability - max no. of devices |
Unlimited |
63 |
127 |
1 |
PC Interface |
GigE NIC or LOM (LAN on the motherboard) |
PCI card or motherboard |
PCI card or motherboard |
PCI framegrabber |
Table-1: Comparison of Digital Camera Interfaces
(Source: Pleora Technology)
|
All of this is possible due to the continued advancement of Ethernet technology, and its tremendous commercial success. Standardized in June of 1998, Gigabit Ethernet offers similar characteristics to well known Fast Ethernet (10/100Base-TX), but it is 10-times faster. Initially deployed in local area network backbones and server connectivity, the decreasing cost of Gigabit Ethernet, has significantly expanded its use in recent years.
Gigabit Ethernet has a maximum transmission speed of 1Gbps (or 1000 Mbps); using familiar RJ45 connectors attached to inexpensive Cat6 (or Cat5e) unshielded twisted pair cabling, capable of connections of up to 100m. More importantly though, is the ability of Gigabit Ethernet to carry a larger data payload of 9000 bytes as compared to the 1500 bytes data payload of previous generations of Ethernet. These “Jumbo Frames” allow more efficient transmission of large blocks of data, such as images, while reducing processing overhead by attached cameras and PCs.
Utilizing Gigabit Ethernet, distances between any two components is at least 100m, a ten-fold improvement over previous machine vision technologies. With a single Ethernet switch placed between a Gig-E camera and a PC, distances of 200m can be achieved. For longer distances, fiber optic cabling may be employed, along with the appropriate Ethernet switch or media converter.
A more interesting result of the adoption of Gigabit Ethernet for Gig-E Vision is the introduction of networking to machine vision systems. Connections between PCs and cameras are no longer point-to-point connections – they are networked. This means it is possible to create systems consisting of multiple cameras and multiple PCs. While the advantages of connecting multiple cameras to a single PC, without the need for multiple frame grabber cards is obvious, Gig-E Vision allows video images from a single camera to be simultaneously sent to multiple PC for distributed image processing.
Like many industrial technologies, Machine Vision spans a wide range of market segments and applications. Several of the market segments showing strong growth for Gigabit Ethernet include automated inspection equipment, medical imaging, intelligent traffic systems, optical character recognition, and public security systems. All of these segments share a need for fast acquisition of high resolution images that are processed by PC-based systems. |
 |
 |
 |
 |
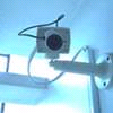 |
Inspection systems |
Medical
Imaging |
Intelligent
Traffic Systems |
Character Recognition |
Public
Security |
|
As an illustration of the capabilities of Gig-E Vision system capabilities, consider its use for automated inspection of product on high-speed beverage bottling line. To ensure quality and safety of the finished product, each bottle must be inspected to ensure product level, proper label application, and secure bottle cap installation. Operating as speeds of hundreds of bottles per minute, this is an obvious Gig-E vision application.
The use of Gigabit Ethernet allows multiple cameras to be connected to a single PC-based vision processing system. Since food and beverage equipment needs periodic sanitary wash down, Ethernet (with allowable distances up to 100m) allows the cameras to be placed in optimum locations, with the PC located where it can be best protected from caustic solutions and machine vibration.
Gig-E Vision compliant cameras and PC-based vision processing software, provide high speed image processing to OEM equipment suppliers and manufacturers, with the flexibility, ease of deployment, and cost-effectiveness required for today’s machine vision applications. |
 |
|
Copyright © 1983-2010 Advantech Co., Ltd. All Rights Reserved. |
|