Hard Drive Manufacturing Quality Control System
Production Automation
Location: Malaysia |
|
Project
Introduction:
Many electronic device manufacturers use machines with PLCs as controllers that need to be able to communicate with a central server for auto process sequence control. A major hard drive manufacturer in the US was facing problems with the communication between their older PLCs and their new server. They desired an automated system that could easily handle communications with the server and provide their engineers with an easy-to-use interface to monitor their HDD manufacturing. |
System
Requirements:
Charging machines are an integral part of the lapping plate process at many major HDD manufacturers. Previously, this customer had been using a manual lapping plate quality control system which depended on the engineers to verify each plate had been charged before being sent to the polishing machine, which was causing many of their HDD’s to be defective. Furthermore they had recently purchased a new server and found that many of their legacy PLC’s were having trouble communicating with it. They needed to automate their quality control process with a reliable system that could communicate with the production server to guarantee quality control for their HDDs.
Project
Implementation:
|
PCI-1761 |
8-ch Relay and 8-ch Isloated Digital Input Card |
|
FPM-3120G-RAE |
12.1" SVGA Industrial Monitor with Resistive Touchscreen |
System
Diagram:
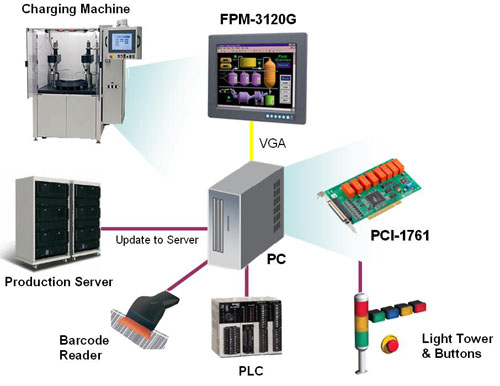
System
Description:
The new system is designed to have auto select recipes, trace and record functions which the original PLC could not do. Advantech provided the FPM-3120G-RAE as the HMI and the PCI-1761 to connect to the EMO, safety door switch, On/Off buttons, light indicator, alarms and signal control. Every lapping plate has a unique barcode which is scanned and sent to the server to verify the process. After the process has been verified, the system will continue running the process or generate an error code if the lapping plate has not been sent to the charging machine.
Conclusion:
The new system successfully automates the quality control process, significantly increasing the reliability and efficiency of their entire production line. Additionally the new HMI device provides engineers with an easy-to-use interface for monitoring and managing the manufacturing process. Furthermore, the new PC-based system provides a larger memory and an open architecture that is easier for programming and expansion.
|