Train-driving Simulator Optimization Using Advantech’s
Distributed Control System
Project Introduction: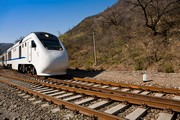
In recent years, China has invested heavily in railway construction. The rapid development of railway systems has increased demand for qualified professionals in the railway industry, especially locomotive engineers. Advantech has previously developed a train-driving simulator to train and instruct new railway workers. Through simulating the conditions and surroundings of train operation, the train-driving simulator provides a highly realistic virtual driving environment. Using this system to instruct train drivers eliminates the need to use actual railway facilities for training, as well as negating the risk to safety of allowing a theoretically knowledgeable but inexperienced new driver actually operate trains. Safe, economical and unhindered by environmental or weather conditions, the train-driving simulator can significantly enhance the effectiveness of training programs for railway workers.
System Requirements:
The train-driving simulator is a system that utilizes computer technology to control and simulate train-driving operations in real time. This system is especially useful for simulating emergency incidents and breakdowns/malfunctions, and can be used to provide train drivers with safe, effective training. The system accurately simulates the driving of a train, allowing trainees to experience “real-life” conditions. This simulator can be used to enhance the skills of train drivers and instruct learners in how to correctly react to a variety of hazardous situations.
For many years, our customers have been using Advantech’s Input/Output card solutions in training programs for railway workers. This simulator is installed in a 10m 2 front compartment and the driving equipment is in front of and on both sides of the driver’s seat. The basic requirement is to use the I/O board and module to read data. However, as the increasing complexity of the system has increased the number of I/O cards required, wiring and cabling work for the overall system has become an extensive and tedious task. Many customers have expressed their desire for a practical solution that streamlines the system while maintaining its original functionality.
Project Implementation:
IPC-610H |
4U rackmount chassis with visual & audible alarm notification |
APAX-5070 |
Modbus/TCP communication coupler with high density I/O, flexibility, scalability, and hot swap functionality |
APAX-5017H |
12-ch high speed analog input module
|
APAX-5028 |
8-ch Analog Output Module |
APAX-5040 |
24-ch digital input module |
APAX-5046 |
24-ch digital output module |
APAX-5060 |
12-ch relay output module |
System Diagram:
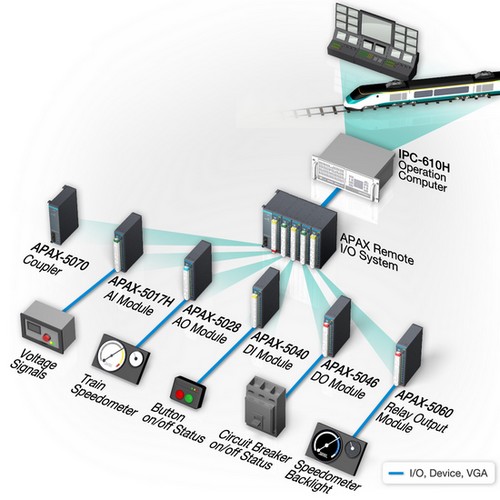
System Description:
In response to customer needs, Advantech developed a distributed control system. The industrial personal computer IPC-610H is used as the monitoring host platform, and is integrated with an APAX high-density I/O module to read both analog and digital data.
As the host platform, the IPC-610H provides the operational screen for train control and processes various elements, such as simulation of scenery on the train route, scene changes, speed control, emergency incidents, etc. The APAX-5070 (Modbus/TCP coupler) serves as the communications bridge, connected to the IPC at one end and the I/O module at the other to obtain, store and transmit data. This special internal bus design facilitates operation through a distributed configuration.
In order to conduct an actual simulation of the control system, this system uses the APAX-5017H high-speed analog input module, which can capture the voltage signals of the power device. The APAX-5028 is applied for outputting analog signals to control the train speedometer. The APAX-5040 is used to detect the on/off status of the switch while the APAX-5046 module can control alarm indicators and the on/off status of the circuit breaker. In addition, APAX-5060 controls equipment requiring greater power, such as the switch of the speedometer backlight. Through the characteristics of the APAX modules, including high-density I/O, flexibility, scalability, and hot-swapping, customers can easily construct remote input and output systems.
Conclusion:
Advantech provides the excellent distributed system that enables configuring I/O modules according to the location of different equipment, thus reducing the need for cables by facilitating remote control. This simplifies the task of wiring or cabling, enhances system efficiency, while also reducing the costs borne by the customer. |