Salt Vacuum Evaporation Monitoring & Control System
Facility Monitoring System
China
|
|
Project Introduction:
While the natural energy of the sun can be used to evaporate brine in hot countries, elsewhere white salt is produced by evaporating brine in pressure vessels. The first plant with a vacuum evaporation system was completed in 1931. Construction of plants with the present type of system began around the mid 1950s. The manual work required to boil kettles was replaced by inspection work such as monitoring and operating devices. One of Advantech's customers in China was looking for a monitoring and management system to control the vacuum evaporation process in thier plant. |
System Requirements:
The vacuum evaporation system is based on the principle that lowering the air pressure lowers the boiling point. The air pressure inside the evaporation system was lowered and steam generated from each of the evaporation sections was used as the heat source for the next evaporation section. System requirements included:
- Liquid level control in one to four evaporation pots, pressure control in an effect heating chamber, mixing brine volume control and temperature control of the brine
- Timing slushing equipment for the second vapor and transmitter tap
- Support for both automatic and manual control while the former is automated
- Remote manual operator and volume accumulation.
Project Implementation:
|
ADAM-5510KW
|
4-slot SoftLogic Controller with RS-485
|
|
ADAM-5017
|
8-ch Analog Input Module |
|
ADAM-5024
|
4-ch Analog Output Module |
 |
ADAM-5068 |
8-ch Relay Output Module |
|
IPC-610
|
4U 15-Slot Rackmount Chassis with Front-accessible Fan
|
System Diagram:
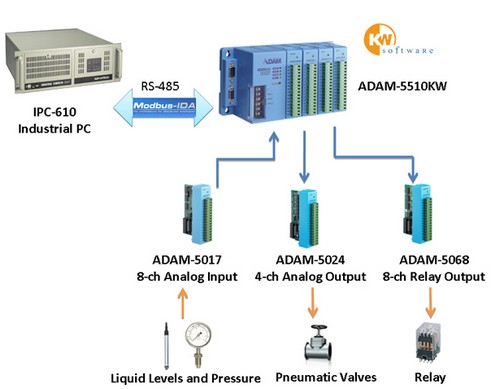
System Description:
A typical vacuum plant consists of a series of closed cylindrical vessels, or 'effects', containing steam chambers, which in turn contain a number of tubes. Vacuum salt making equipment has 70 I/O nodes: 45 analog input AI (platinum resistance thermometer signal is included); 9 analog output AO; 16 on-off output DO. In consideration of the above requirements, this system was setup with Advantech's ADAM-5510KW SoftLogic controller and IPC-610. Through RS-485 serial port and Modbus protocol, the lower and upper computer together make up a discrete control system.
ADAM-5510KW is a PC-based SoftLogic controller, which features its own CPU and various I/O modules, such as ADAM-5017, ADAM-5024, ADAM-5068 and ADAM-4024 can be integrated into the system to provide data acquisition and control output. IPC-610 is equipped with configuration software for real-time monitoring. Multiprog is also installed to realize ADAM-5510KW programming, compiling, downloading and debugging. The ADAM-5017 acts as a field transmitter to convert physical signals, such as liquid levels and pressure. The ADAM-5024 measures the current input of the pneumatic valves. The ADAM-5068 Relay Output Module operates the relay through automatic and manual control.
Conclusion:
In the vacuum salt making process, Advantech's solution was implemented to feature powerful and reliable componets with advanced management and control technologies. ADAM-5510KW is integrated with configuration software, realizing PID functions, and providing fast development and debugging of the whole control system. This system can ensure a precise signal acquisition and output control as well as an excellent auto PID control mode. This control system features mature technology, high stability, rich functions and low maintenance, thus it can play an important role in control automation for many industrial processes and provide considerable economic benefits to a wide range of enterprises.
|