Project Introduction:
With a global increase in the demand for green energy solutions, the use of solar cells (aka solar panels) is quickly spreading to residential and commercial facilities, resulting in an increase demand in manufacturing and production equipment. The essential steps in the production process of a solar panel include: Pick-and-Place, high-speed movement, accurate positioning and fixed plug-in fitting. But it is the dislocation and false welding of components that are greater obstacles in the inspection procedure. Therefore, customers need to adopt high-speed multi-axis motion control with a machine vision system to improve their production efficiency.
|
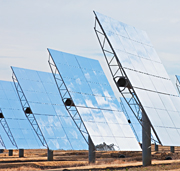 |
System Requirements:
Through the use of Pick-and-Place technology, the solar cell will be placed on conveyer belt and then put in the pre-setting device or storage box where a sensor detects the cell. This traditional procedure is a closed control structure with complex tools for programming and involves a lot of time and money if it needs to change the process or expand the interfaces. In addition, the maintenance costs are far higher than PC-based control systems that lead to low productivity and high production costs. As technology advances, building a flexible PC-based motion control system becomes a primary consideration of many companies since, by using a variety of technologies:
- A high-speed motion control module - accurately executes Pick-and-Place tasks and puts the known good cell into the cassette.
- A digital input / output module - acquires the sensors' signals on the conveyor belt and detects the cell's location and surrounding states.
Project Implementation
:
UNO-3084
|
Intel® Core™ 2 Duo Automation Computer with Dual DVI, 1 x PCIe, 3 x PCI and FireWire |
PCI-1202U
|
2-port AMONet RS-485 PCI Master Card |
AMAX-2241/PMA |
4-axis AMONet RS-485 Motion Slave Module for Panasonic Minas A |
AMAX-2752SY |
32-ch Isolated Digital Input Slave Module |
AMAX-2754SY |
32-ch Isolated Digital Output Slave Module |
AMAX-2756SY |
16/16-ch Isolated Digital Input/Output Slave Module |
System Diagram:
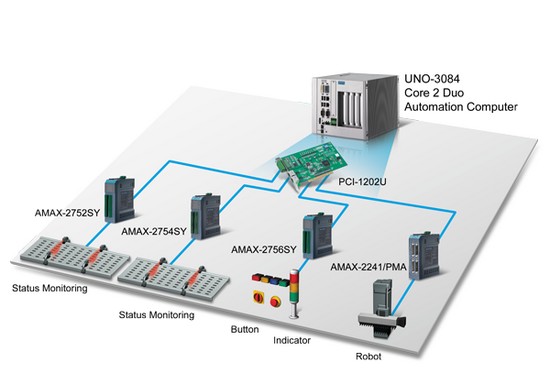
System Description:
The UNO-3084 dual-core embedded controller - integrated with a PCI-1202U AMONet communications card - can provide real-time control device for a Pick-and-Place mechanism with 20 Mbps transfer rate (scan 1024 digital I/O channel within 1.04ms or manage up to 256 axes for motion control). The AMAX-2752SY/2754SY/2756SY digital control module can deliver the devices’ I/O control signal to the control center via AMONet communication. As a control medium between devices and control center, the AMAX series supports immediate transmission which not only transmits the production states but also receives instructions from the control center to adjust and precisely control the operation.
Conclusion:
Using PC-based AMONet solution (integration of UNO-3084 and PCI-1202 AMONet, and AMAX series - data acquisition and motion control), the process can be divided into multiple areas for effective control. Meanwhile, the whole system can lessen the wiring installation time of electromechanical systems, improving performance, decreasing error rates, and reducing costs. The operator can more easily transform and upgrade the production process. In addition, Advantech's AMONet solution also offers the following advantages:
- A suitable solution for automated production systems of large equipment such as solar energy and LCD panels.
- Can be integrated with MES or CIM systems
- Reduces the problem of signal attenuation due to longer electrical wiring
- Lessens the assembly time and wiring check to improve the time effectiveness of equipment assembly
|